Thank you for joining. Depending on who you are and your involvement with fire stopping, you may find value in one or more of the following sections. Some sections are technical, and others are more practical. The sections I cover in this post are:
- Fire stopping basics.
- What is a fire stop ‘listing’?
- What are the different types of fire stop ratings?
- What fire stop rating do I need?
- What to consider when installing fire stop systems.
- What to consider when reviewing fire stop systems.
- Additional reference information.
Fire Stopping Basics
Fire stopping is required by building codes to maintain the integrity of fire separations and limit the spread of fire and smoke in a building. They are used wherever there are gaps created in an otherwise continuous fire separation – common examples are:
- Service penetrations – pipes, cables
- Joints between assemblies – wall-ceiling joints
- Blank openings – unused holes in assemblies
Fire stop systems come in different configurations. Most modern fire stop systems use an intumescent as the primary component, which swell and insulate when exposed to heat. Intumescent caulking and collars are most common.
Fire stop systems are passive fire protection systems, meaning they do not require any external power or human intervention once installed. This means it is important to follow a fire stop system design that has undergone fire testing, to ensure proper performance in a fire scenario.
In Canada, fire stop systems are tested to CAN/ULC-S115, “Fire Tests of Firestop Systems.”
It is important to remember that the intumescent caulking used in most fire stops does not have a rating on its own, but is assigned a rating based on the entire tested system. This will include elements such as the surrounding assemblies, gap sizes, and service penetrations.
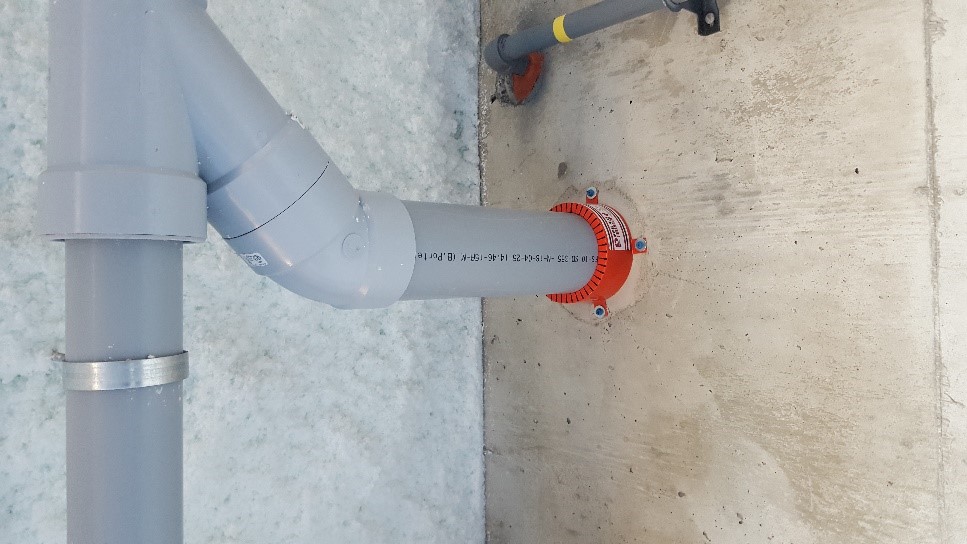
A useful analogy when thinking about fire stop systems is baking. In fire stopping, like in baking, it is important to follow a recipe (listing or tested system in this case). An inexperienced baker could easily mix ingredients into something that resembles cake batter; though if the proportions are off, their cake will not turn out well. Firestopping is similar – it is easy to slather “fire caulk” over a penetration, but if a recipe (listing) is not followed, it is difficult to say how it will perform when it is baked (in a fire).
What is a Fire Stop ‘Listing’?
The most common way of ensuring a fire stop system meets the testing requirements is through a “listing”. Listings are confirmation of testing and/or quality by a third party. In the case of fire stop system, a listing will at least indicate the test standard that was used to evaluate the system, the fire rating achieved, and any installation instructions or limitations (penetrations types and sizes, surrounding assemblies, etc.).
The Canadian building codes do not specifically require a listing; they only require that a specific test is followed (CAN/ULC-S115 in this case). However, following a listing is the easiest and most common way of demonstrating the testing requirements were met.
What are the Different Types of Fire Stop Ratings?
There are a few different types of ratings for fire stop systems that are assigned durations based on the test criteria in CAN/ULC-S115. In general, they can be described as follows:
- F rating – Fire stop remains in place for rated duration and does not allow passage of flaming.
- FT rating – Meets the requirements of an F rating, but also limits the temperature rise on the unexposed side of the fire stop.
You may also encounter FH or FTH ratings, but these are not required by the Canadian codes. The H is used to indicate the fire stop system passed a hose-stream test. L ratings may also be provided on listings, which indicate the air leakage through a fire stop system (also optional).
What Fire Stop Ratings Do I Need?
The rating required for a fire stop system will depend on where it is used. These requirements are discussed primarily in Article 3.1.9.1.
Fire Separations – F rating, based on fire protection rating for closures (see Table 3.1.8.4 in the Building Codes)
Fire Separation Rating | F Rating |
45 min | 45 min |
1 h | 45 min |
1.5 h | 1 h |
2 h | 1.5 h |
3 h | 2 h |
4 h | 3 h |
3.2.1.2 slab (basement storage garage/parking as separate building)
Firewall – FT rating, 2 h or 4 h based on the firewall rating
Combustible drain, waste and vent piping – F rating, based on fire-resistance rating of the fire separation, and subject to a 50 Pa pressure difference during the CAN/ULC-S115 test (see example below)
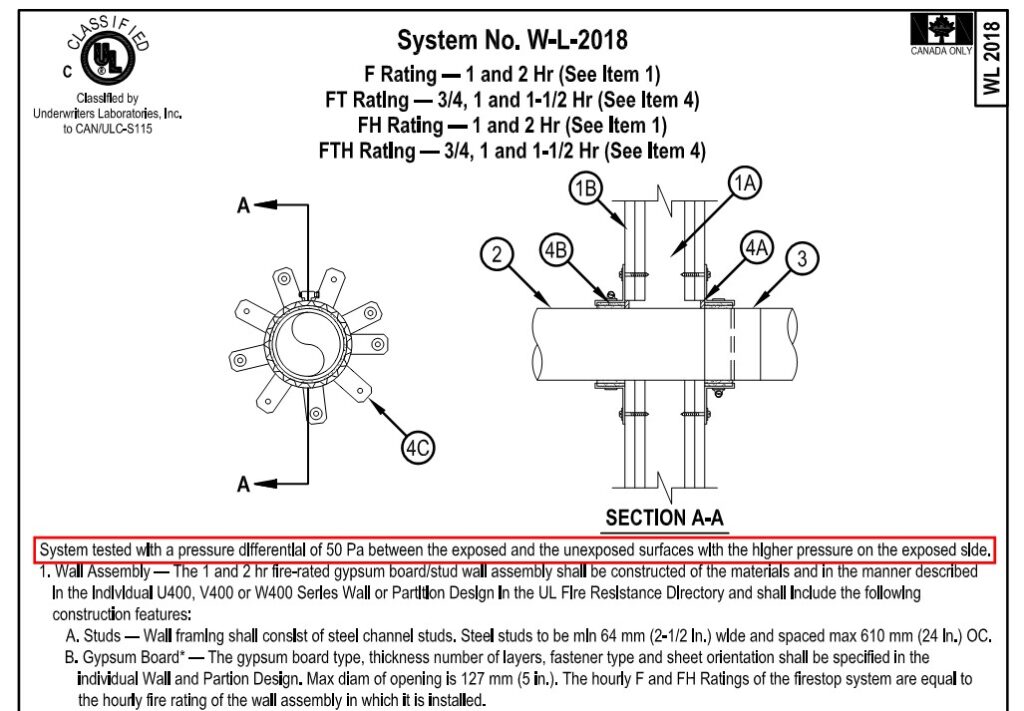
Horizontal service space that passes over a vertical service space, and not divided at vertical fire separation (Sentence 3.1.9.1.(3), see figure) FT rating, not less than horizontal service space fire-resistance. If you’re not sure you’ve ever applied this, you’re not alone. I describe it further in the next section.
When Would I apply Sentence 3.1.9.1.(3)?
This scenario is common in wood frame construction, where vertical suite separations may terminate at the underside of a gypsum board ceiling. In that case, the gypsum board ceiling membrane needs the same rating as the wall assembly. This scenario is unique since the ceiling rating is achieved through the gypsum board alone (as opposed to the complete assembly). Fire stops in this scenario are required an FT rating over the membrane only, as opposed to the full floor assembly, to prevent ignition in the concealed space.
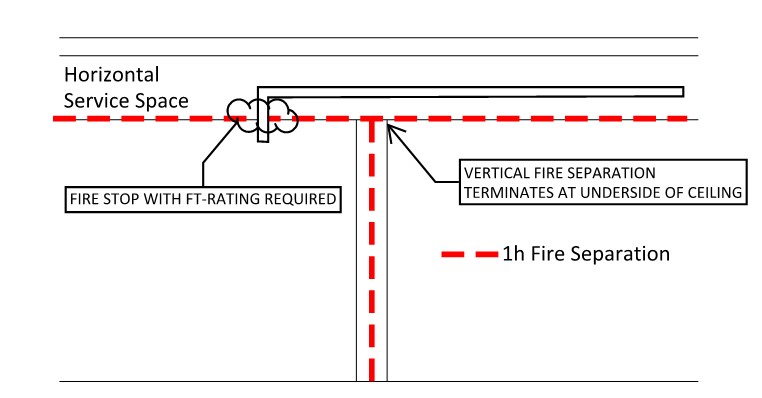
To my knowledge, there are no listed systems to address these membrane only fire separations. A common approach for pot lights and other fixtures is to “box out” with gypsum board and apply intumescent caulking to any small electrical penetrations of the drywall box. Strictly speaking, this approach is not code conforming, though it seems to be common practice accepted by registered professionals and authorities having jurisdiction.
What to Consider When Installing Fire Stop Systems
Products are to be installed by a competent person/contractor strictly in accordance with the manufactures’ specifications. When installing a fire stop system, some of the things you should consider are:
- What product was specified? Each product will have its own requirements and they are not interchangeable. This is true even for different products from the same manufacturer.
- In what type of assembly is it being used? Each situation will require a unique system, though they may be very similar in practice. Is it a wall or floor/ceiling assembly? Is it concrete, steel stud, wood stud, etc.
- What types of penetrations are allowed? Steel pipe, copper pipe, PVC pipe, etc. What are the maximum sizes?
- Follow maximum gap sizes allowed.
- Are any other products needed, other than the caulking material? Mineral wool insulation is often required as a forming and/or insulating material.
- How much fire stopping material is needed? More is not always better, as it could affect how the product cures.
- Ensure the penetrations are at 90° to wall/floor assemblies, unless angled penetrations are specifically allowed by the listing.
What to Consider When Reviewing Fire Stop Systems
When reviewing a fire stop system, some of the things you should consider are:
- Verify that the system is tested to CAN/ULC-S115, “Fire Tests of Firestop Systems”
- Does the fire stopping product (brand, type) used on site match with the product in the listing?
- Where is it used? This determines the rating, as discussed above.
- Do the wall, ceiling, roof assemblies, etc. in the listing match those in your application? Consider the fire rating of elements, structure type and sizes (wood studs, steel studs, concrete wall or floor), etc.
- Penetration systems. Is the type of penetration permitted (steel pipe, copper pipe, PVC pipe, etc)? Is the size and number penetration permitted?
Additional Information
A useful resource for additional information on fire stops is an NRC publication titled “Best practice guide on fire stops and fire blocks and their impact on sound transmission.” It goes into much more detail on specific types of fire stop systems and scenarios. Find it here.
The City of Regina also recently released a very informative advisory on fire stopping. You can read that here.
Food for Thought
Here are a few additional though provoking comments:
- Fire stop listings reference specific floor or wall assembly listings. If you are using a generic rated assembly (floor or wall), such as Appendix D in the Canadian building codes, you are technically deviating from the fire stop listing. This seems to be commonly accepted, or not considered (I am not sure which). This might be a barrier for fire stop systems involving mass timber assemblies such as CLT, since there are currently no listed CLT floor assemblies (as far as I know).
- Fire protection ratings vs. fire-resistance ratings. This is an important distinction to understand that often causes confusion (both are defined terms in the Canadian building codes). Note that drain, waste and vent piping requires a fire stop with an F rating based on the fire-resistance rating of the assembly.
- Fire stopping in Part 9 buildings. The fire stopping requirements indicated in Part 9 are a bit different than Part 3 and can be interpreted as being more relaxed by allowing generic fire stop materials such as mineral wool or gypsum plaster. Problems with fire stopping frequently arise when contractors with experience primarily in single family or small Part 9 buildings venture in the commercial and Part 3 construction.
7 Responses
Thanks for the post!
Question: when there are multiple requirements, do you apply the most strict of the fire stopping requirements? For example: if combustible DWV is penetrating a horizontal fire separation above a storage garage that is considered a separate building the following would be considered:
– Combustible DWV fire stopping requirements: F rating equivalent to FRR of the horizontal fire separation, with 50 Pa of pressure on exposed side
– Storage garage as separate building fire stopping requirements: FT rating equivalent to FRR of the fire separation.
So would the requirements in this scenario become: FT rating equivalent to FRR of the fire separation, and 50 Pa of pressure on the exposed side?
I’ve heard there are challenges with finding listings that can provide this information, so was wondering if others have thoughts on this as well. Thanks!
Thanks for reading! And good question.
I would say that your analysis is correct. The combustible DMV requirements are additional requirements that should be met along with the FT requirement if both are applicable. I have not run into that particular scenario in the field, but I can see how it could be a challenge.. From a quick search, there seem to be some listings that meet this but it obviously will depend on the particulars of the scenario. I would expect cast in place devices and sleeves to be needed in most cases.
Thanks for the reply and confirmation of this approach!
Thanks for this post Marc! I’m an architect in a small town and one scenario I often run into is that the majority of assemblies I encounter are unique to any listing I can find. Commonly, I will find a listing that is 80 or 90% similar to the assembly being proposed but there are some minor differences. This gets to your first point under ‘Food for Thought’. Unless I can convince builders to change the assembly, often difficult to do, especially if it’s an existing assembly, the best option is to follow the requirements of a listing that is as close as I can find and go with that. I understand that, technically, it doesn’t meet the listing and therefore, it can’t be used but I’m not sure how else to approach it. This is a problem I have encountered several times and particularly in older buildings that people are changing and need to be upgraded to meet current code. Wondering if you can provide some suggestions or guidance on how to deal with this?
Hi Nelson, sorry for the delayed response here. Unfortunately, I don’t think there is a straightforward solution. This is definitely an area that is difficult, especially when dealing with existing buildings. When dealing with existing buildings, I think it is important to remember that the building code was not written with upgrade to existing buildings in mind. In some cases, full compliance may not be achievable without considerable expense, so the code has some relaxation in this regard (A-1.1.1.2.(1) in Division A of the BC Building Code is helpful).
Engineers and Geoscientists BC (EGBC) has put out a practice advisory on this issue: https://www.egbc.ca/getmedia/ec4ff1af-2a62-46e8-8868-ca570eae0e62/Practice-Advisory-Fire-Tested-and-Listed-Assemblies.pdf.aspx
The advisory essentially says that modifications to tested/listed assemblies constitutes the practice of engineering, and that an engineer needs to take responsibility for the modification under seal. Sometimes the fire stopping manufacturer may be able to provide some assistance in this regard, though the EGBC practice advisory notes that many of these companies will not provide a solution reviewed and sealed by an engineer.
I find that compliance with listings in general (be it fire stopping or fire rated wall/ceiling assemblies, etc.) is not well understood by the installers. The listing requirements do not seem to be relayed to the person on site doing the work in most cases, so I am not sure how closely the requirements are followed by industry in the first place. It is definitely an area where more education would be helpful.