Although the annual inspection records can be large and comprehensive documents, there are a few key areas to look at and questions to ask that can tell a story as to whether the annual inspections have been performed properly. As practitioners, we can help owners to understand their responsibilities and to identify when something observed on site indicates to us that the maintenance, testing and inspection program may be inaccurate or noncompliant.
It is important to realize that in most cases, the way we imagine a building will function when we review the drawings, permits, reports etc. (which are created for construction) can be very different from the reality of the occupied building and how it is maintained over time.
An owner is required to confirm that the original design intention, whether relating to life safety, accessibility or inclusion, is still being met from a functional, safety and user-based standpoint. The only way to accomplish this is through a regular inspection, testing, and maintenance program.
This post will:
- Introduce how the Codes regulate testing, inspection, and maintenance programs, and
- Share hints for identifying common flaws in annual inspection reports to understand if the building systems perform the way that they were intended.
Code Application
The types of life safety systems installed in a building and that typically require inspection, testing and maintenance per the Fire Codes are:
- Fire Alarm and Voice Communication Systems for Life Safety
- Sprinkler Systems, Fire Pumps and Standpipe Systems
- Monitoring of Fire Alarm and Sprinkler Systems
- Emergency Lighting and Exit Signage
- Fire Extinguishers and Hose Cabinets
- Fire Doors, Egress Routes and Exits
- Emergency Power Systems (Generators)
- Private Fire Hydrants
- Special Suppression Systems (Kitchen Hood, Clean Agent, Gas and Foam Systems)
Depending on the part of the country you are in, the various Building and Fire Codes will apply as illustrated below:
Being based in Ontario, I am going to use the Ontario Fire Code references in this post – but be sure to check that you are using the appropriate reference for your province.
Responsibilities:
When considering how to apply the Fire Code requirements for inspection, testing and maintenance, it is important to determine the roles and responsibilities for the program:
Owners (and operators) are responsible for achieving and maintaining compliance with the Fire Code per OFC Article 1.2.1.1., Division A, which states that “Unless otherwise specified, the owner is responsible for carrying out the provisions of this Code”. While it is incredibly important to select experienced vendors to undertake the technical elements of the inspections, testing and maintenance program, it is critical for owners to understand their responsibilities and the value that these programs provide.
It is required that the building owner keep copies of inspection and test reports – including corrective measures and operational procedures and are required at the building premises for 2 years. Some inspection vendors provide a certificate; however, this is not recognized by the Fire Code and is not necessary. For example – fire alarm testing, per OFC Clause 6.3.2.2.(4)(a): “a record of each device, component and circuit of the fire alarm that is tested shall be kept in accordance with above”. The Fire Code requires the location sheets be provided, with details for the inspected devices, not just a generic certificate.
Unless otherwise stated, any test mandated by the Fire Code is required at a minimum to record: what was done and the date and it was undertaken. This minimum record-keeping can be applied to the monthly requirements in most cases and can range from detailed monthly reports to simply initials in the fire log book for the date and type of inspection performed. It is considered best practice to have an electronic copy and a hard copy on site of all required fire protection and life safety system design and inspection, testing and maintenance documents. Ideally the records are organized per system type and year, and are easily accessible to authorized persons.
What to look for in Annual Inspection Reports:
The following are some quick observations that you can make of an inspection report that can indicate that more digging is required to verify that the inspections are being undertaken to Code.
My list isn’t intended to be comprehensive, and I’m not implying that any one of these observations would mean that a Vendor hasn’t undertaken their job responsibly – errors can happen. However, if you’re observing numerous issues, and if you can’t find a clear reason then there may be a bigger problem that needs to be investigated. Of critical importance – the life safety and fire protection systems may not have been maintained properly and their integrity and reliability may be in question. As practitioners we can help owners to navigate these investigations and provide our expertise regarding what the Codes require and how the systems are supposed to be tested, inspected and maintained.
- Are there sections in the report that are blank that shouldn’t be, sections left out, systems not noted that are actually in the building? – This could reflect a lack of attention to detail and may mean that parts of the building systems are not being inspected properly, or at all
- Are Vendors referencing the wrong standards or incorrect editions? – It‘s a quick check to see if the standard referenced on their forms matches the current Fire Code edition
- Where smoke sensitivity or battery testing is completed, are readings different year over year or does it look like the values are identical to the last year or other detectors in the building? – Repetitious entries could reflect that testing is not being undertaken properly or that devices have been skipped.
- Do device type legends match the device labels on the location sheets (e.g., does the brand, type and part number in the legend correspond with the information on the location sheet or what is actually in the building)? – Again, this may mean that parts of the building systems are not being inspected properly, or at all
- Is the technician CFAA or ASTTBC number present on the report and do the credentials check out?
- Was testing completed on the same day for areas of a building that usually require special access? (e.g., a detector in a hydro vault that typically requires the building owner to organize access shows as tested, but the building owner never scheduled that access?) – Is there reason to believe that the inspection report is not factual
- Was a time delay recorded for flow switch, and is the delay consistent with typical system expectations?
- Where the sprinkler zones are listed, do they match sprinkler zones identified on the building fire alarm report(s)? – Inspection reports that rely on templates may not suit the building or design of a specific system, it is important that the inspection report reflects the actual design
- In a comparison of year over year reports, are there noted inconsistencies? (e.g., a floor that had a note that a speaker had been removed one year and then the next year its marked as operational) – Again, this may mean that parts of the building systems are not being inspected properly, or at all
- Are the notes and wording on the report identical year over year when that doesn’t make sense? – Were there different inspectors, or had there been changes to building components?
- Are there recurring deficiencies year over year.?– If there is something that shows up as a deficiency one year it is important to look back and see if this deficiency has shown up in past inspections, perhaps a few years back under a different service provider) Deficiencies that are pointed out on one report that have not been rectified by the following year report are of concern.
[convertkit form=1987179]
Understanding Deficiencies
Are no deficiencies a good thing? It might be counterintuitive to think that you want to see deficiencies after your annual inspection, but it’s important to remember that you can expect to have regular items year over year that need maintenance or devices and systems that need to be altered due to the normal changing of how a building is used. Is it possible that year over year there are no problems in a facility, or is it that things are getting passed over or missed?
Is it possible that year over year there are no problems in a facility, or is it that things are getting passed over or missed?
Is a building owner more likely to have a vendor back that repeatedly identifies deficiencies or gives a “clean bill of health” year after year? Perhaps, but the thought of a clean bill of health may be misguided. The constant maintenance and repair work identified in an inspection may reflect a building with correctly maintained fire protection and life safety equipment – what would we like to see in a ‘healthy’ building?
It is also important to be critical of a report. History has shown that in some cases, the skill set of an annual inspection provider can be limited in terms of the types of deficiencies that they can repair: reprogramming of the fire panel, replacement of a sprinkler valve, water supply repairs, etc. It can occur that vendors may only point out deficiencies that they can repair easily themselves and not extensively point out deficiencies that would require them to call in a competitor to complete the service. As such, it is very important that building owners are educated and involved with their service providers to understand the deficiencies listed and how they will be fixed. Another thing to note is that just the fact that a provider has returned to repair some deficiencies, doesn’t mean that they have completed all of them. The building owner needs to follow up and have documentation that shows all of the deficiencies listed have actually been repaired.
After the Report
Once an inspection report has been provided, it’s completeness and accuracy reviewed, and the deficiencies understood – it is very important that the building owner understands their responsibilities. Receiving the report is just the beginning, as I mentioned earlier – the building is like a living environment and the fire protection and life safety systems need to perform throughout the lifetime of that building. The are actions that an owner should do once they receive an annual inspection report:
- The owner needs to ensure that any deficiencies identified in a report are resolved and that building managers and operators understand their responsibility versus the responsibility of the Vendor.
- The owner needs to examine if deficiencies coming from external vendors are consistently observed as being in their area of expertise and be sure to explore other options for repairs.
- The owner needs to understand the importance of knowing what fire protection and life safety systems are in the building and the Code requirements from an inspection and maintenance standpoint.
- The owner needs to ensure building managers understand, use and value an up to date Fire Safety Plan.
- The owner needs to create a binder (or electronic) filing system for all fire protection and life safety system inspection, testing and maintenance report documents and the system must be easily accessible and up to date.
Learn More!
Reading and learning about the requirements is good, but working though an online short course is even better. Gerry’s Precision Course: Life Safety Systems Inspection, Testing and Maintenance is available now.
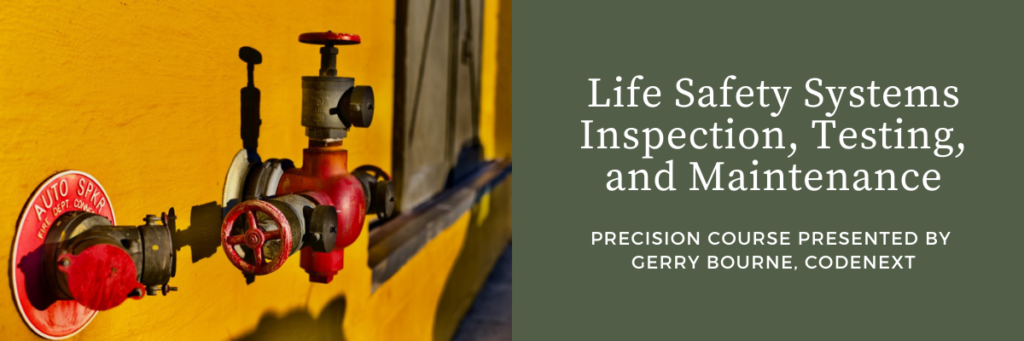
One Response